Производство акустических систем Arslab: репортаж с фабрики Аудиомании в Риге
Рига встретила чистым небом, ярким солнцем, отсутствием суеты и пробок.
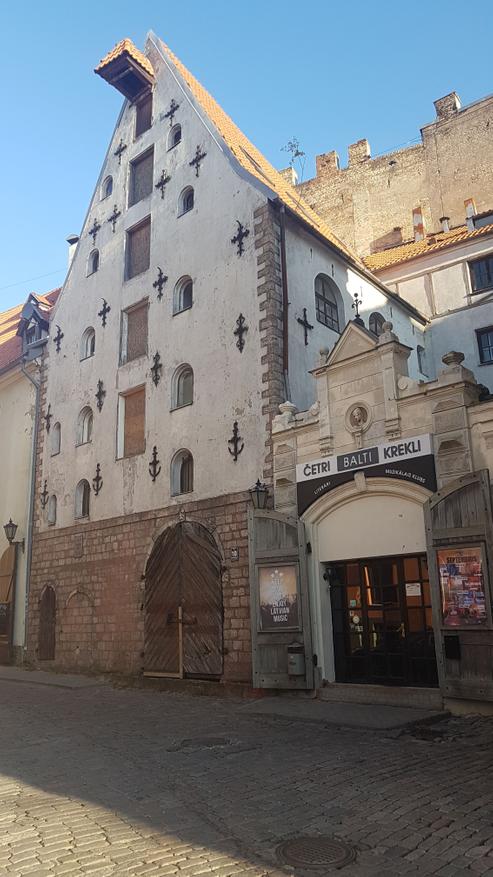
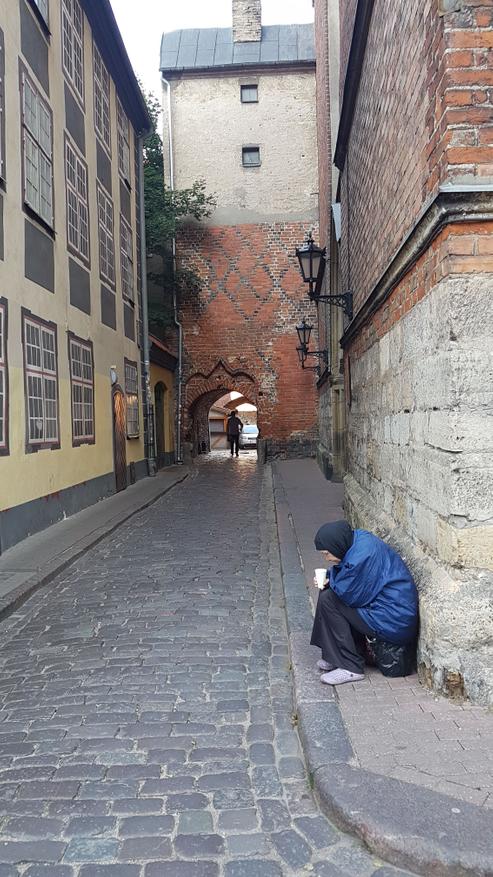
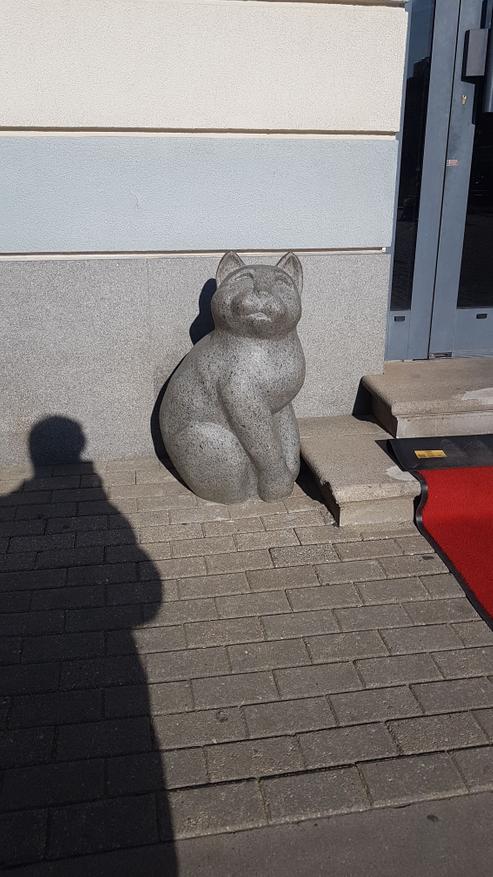

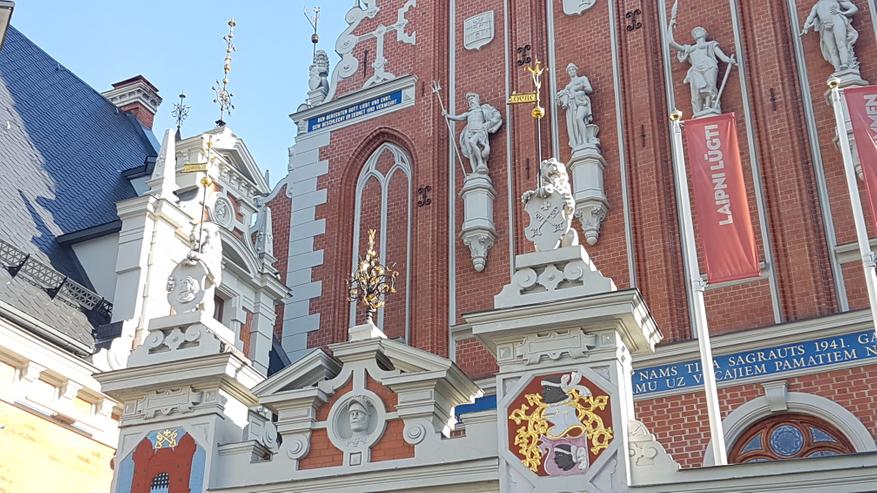
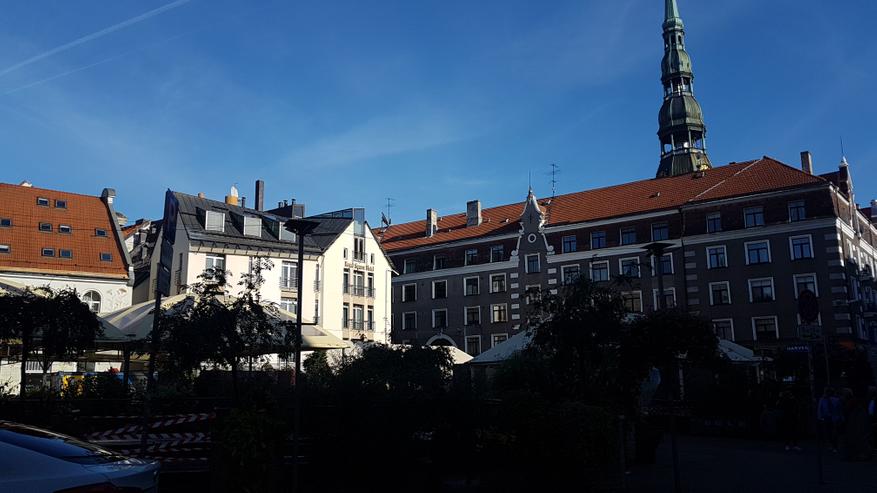
Фабрика расположена в промышленном районе в черте города. Штат сотрудников 15 человек.
При входе на фабрику посетителей встречает небольшая демо-комната.
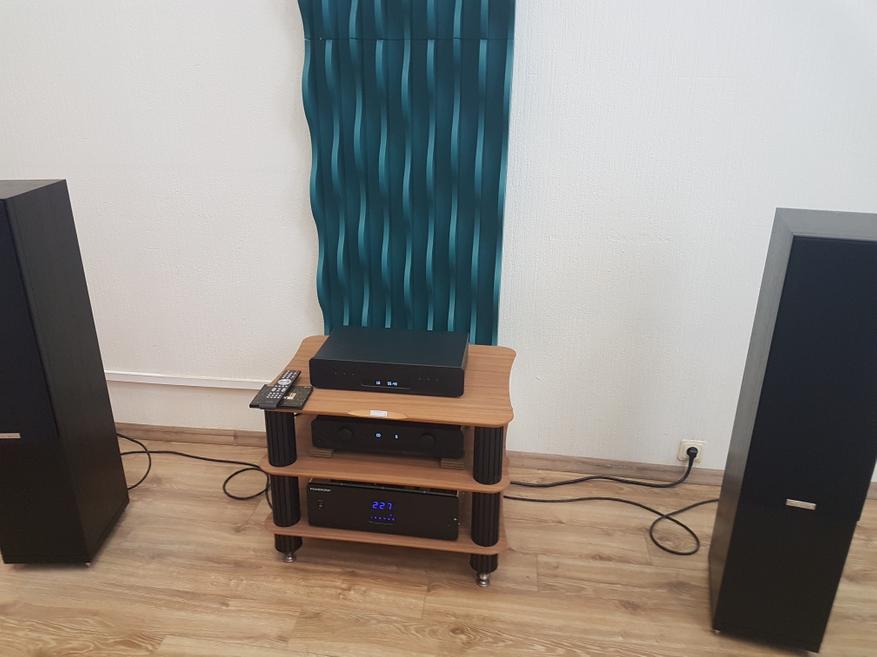
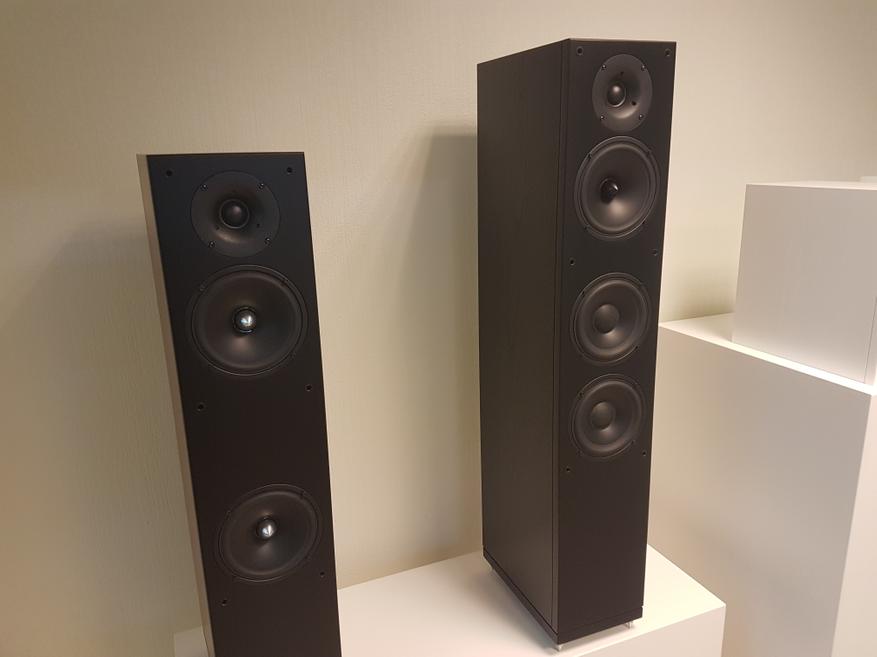
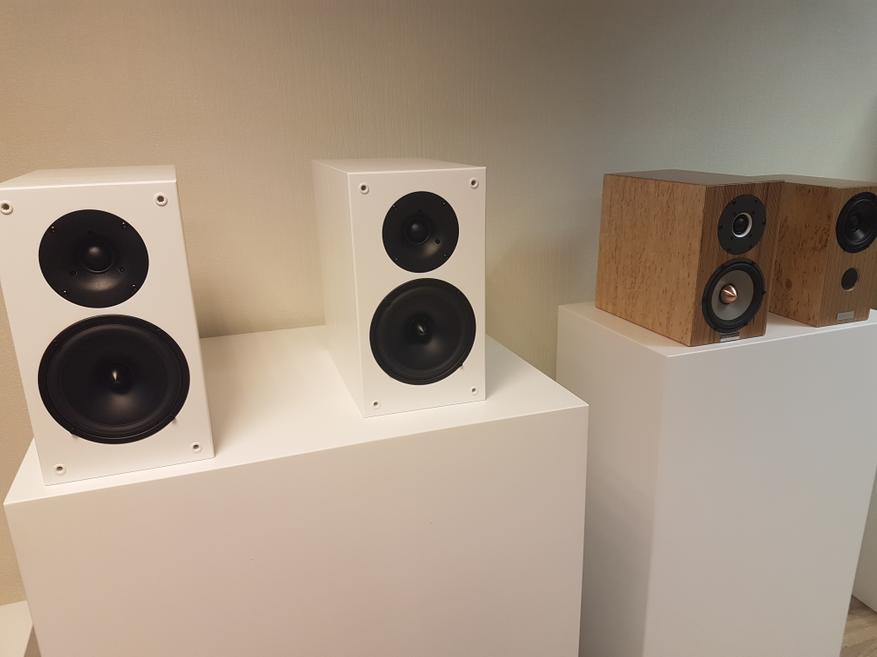
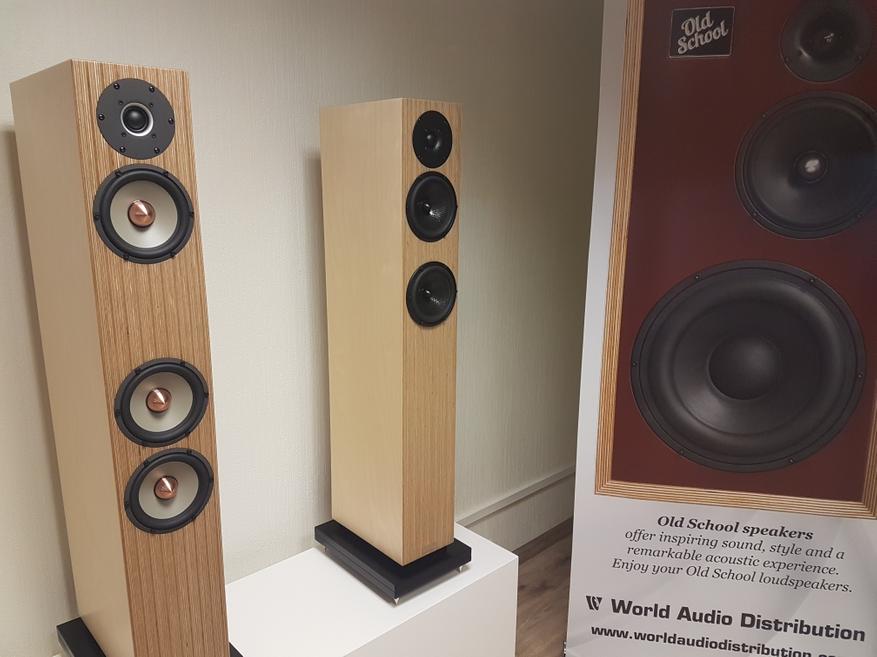

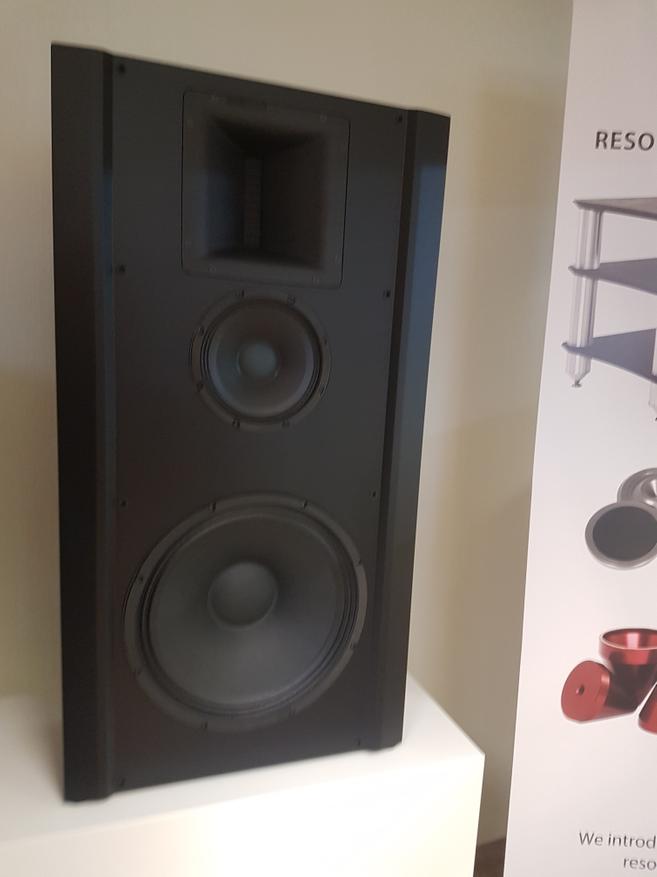
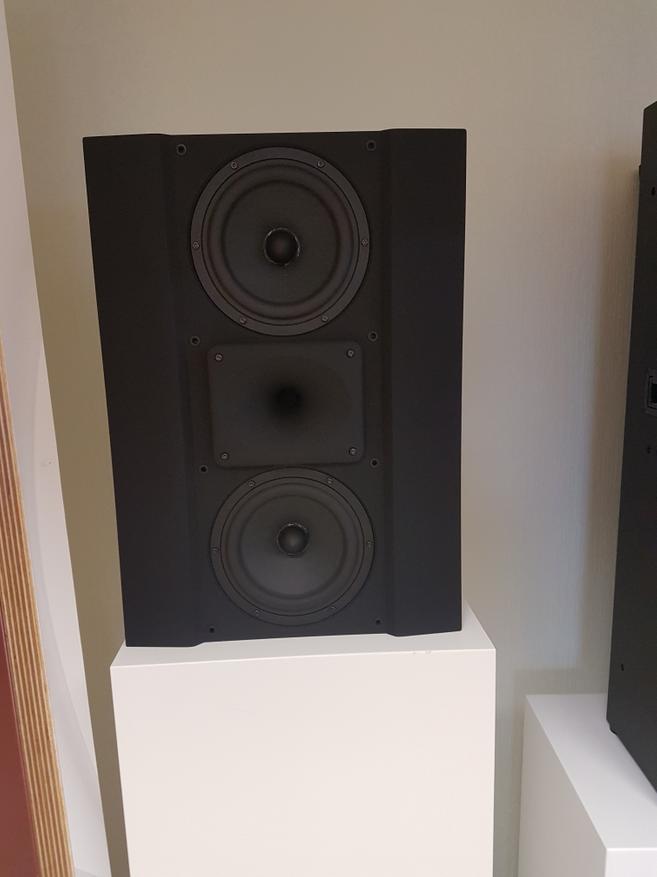
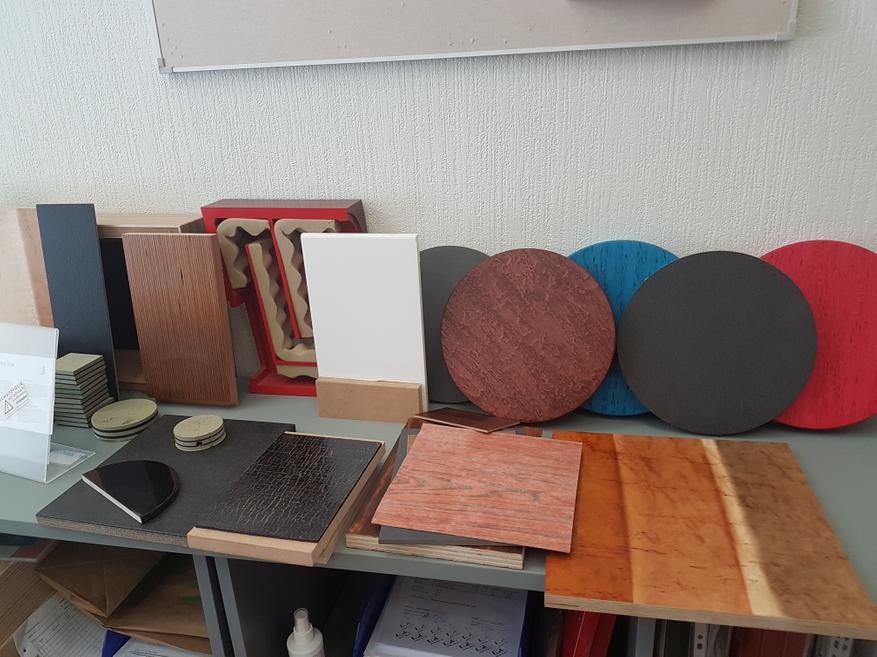
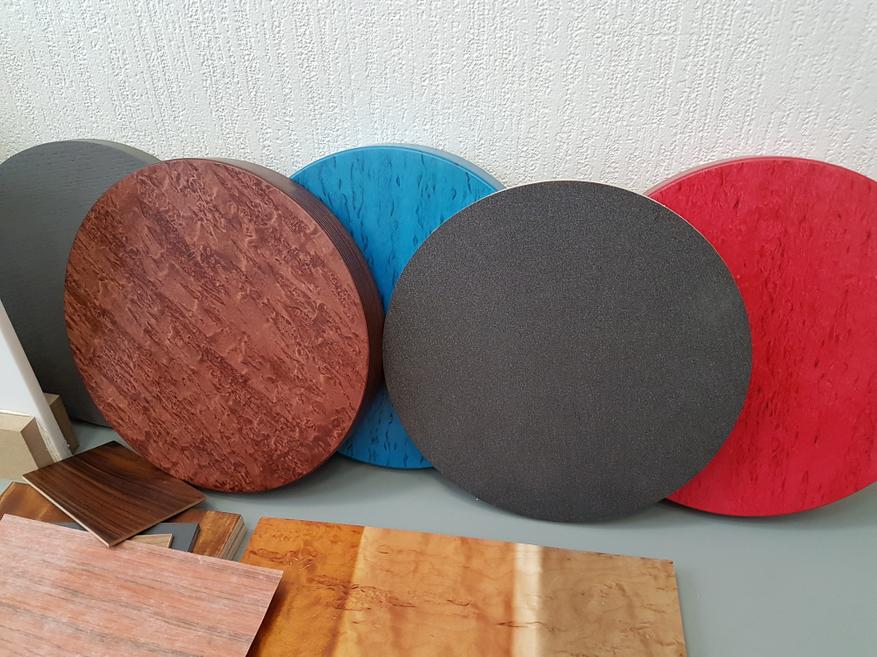
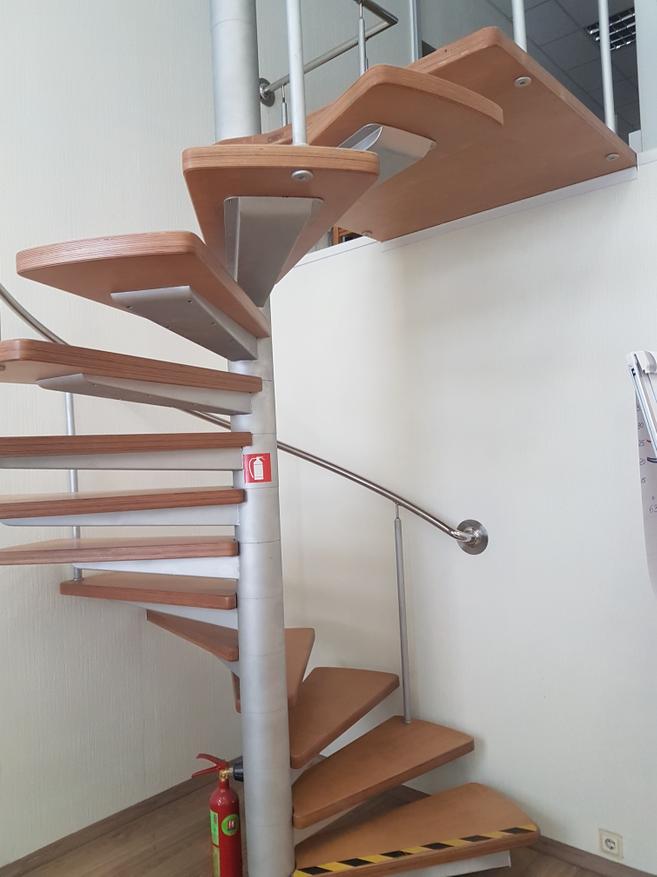
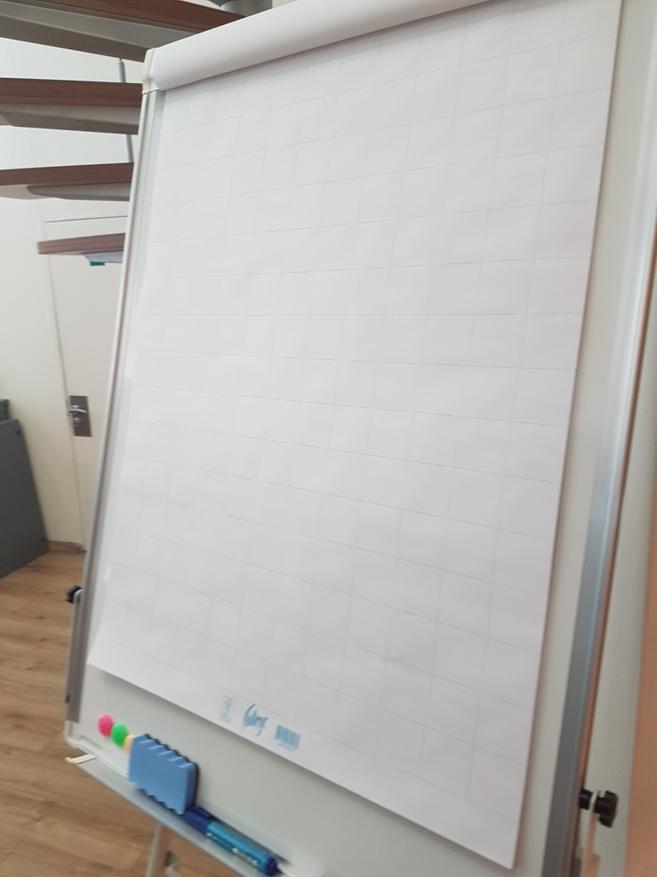
Информационная доска в дальнейшем нам пригодилась для иллюстраций различий акустических свойств различных материалов, используемых при производстве корпусов акустических систем.
Первый цех — производство корпусов. Больше этого цеха только склад готовой продукции. В цеху с потолка в автоматическом режиме распыляется вода для поддержания необходимой влажности воздуха
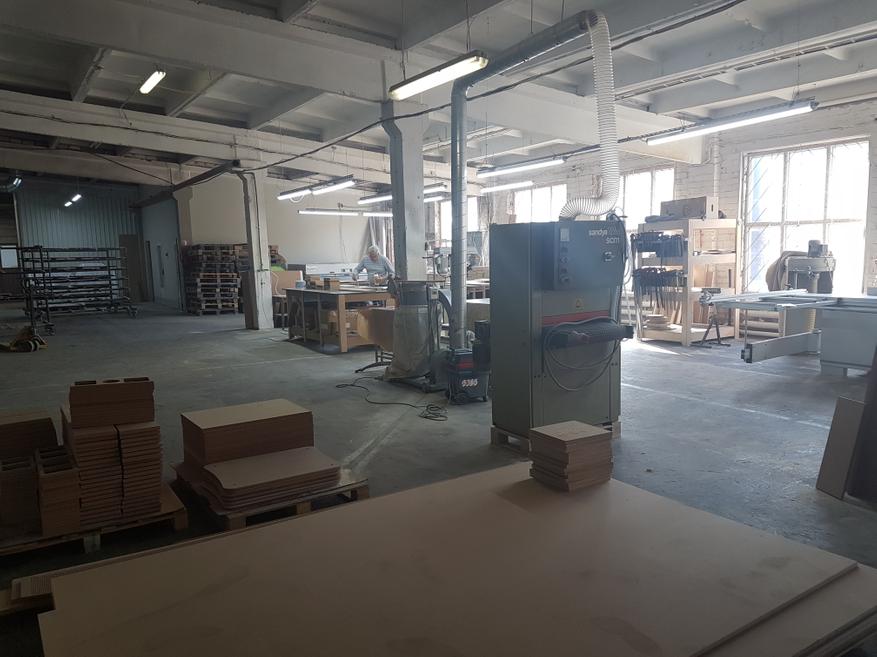
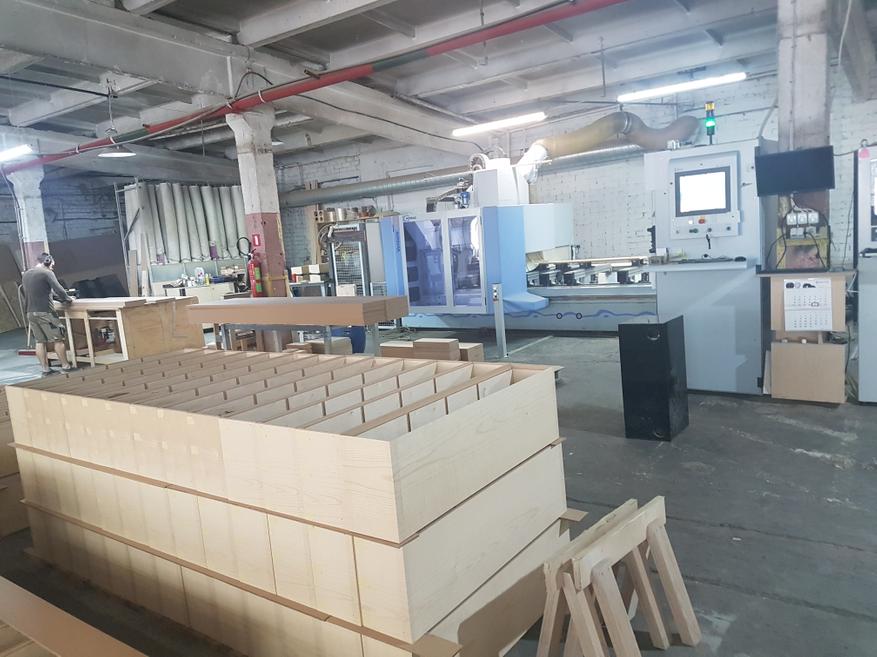
В день моего посещения изготавливались корпуса для модели Arslab Classic. При производстве на фабрике используются высокоточные «пятиосные» немецкие станки, способные в автоматическом режиме менять инструмент для различных операций. Раскрой деталей учитывает все нюансы, включая углы сопряжения для лучшего нанесения и работы клея.
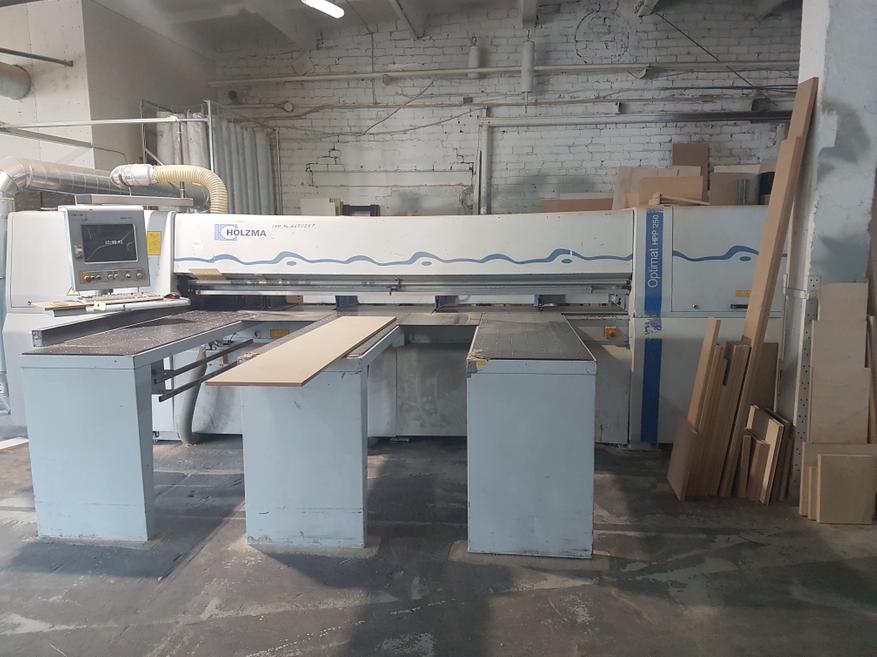
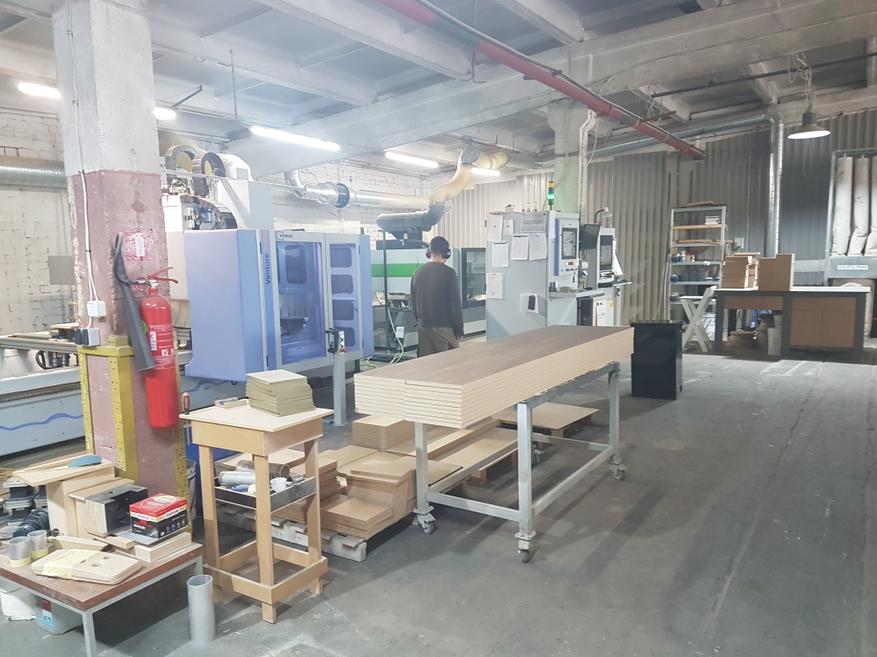
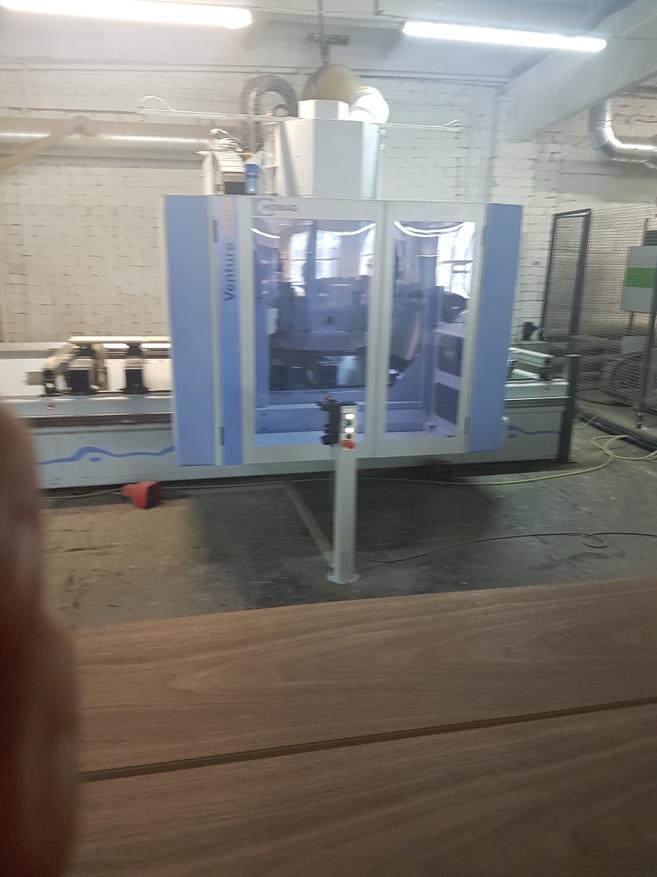
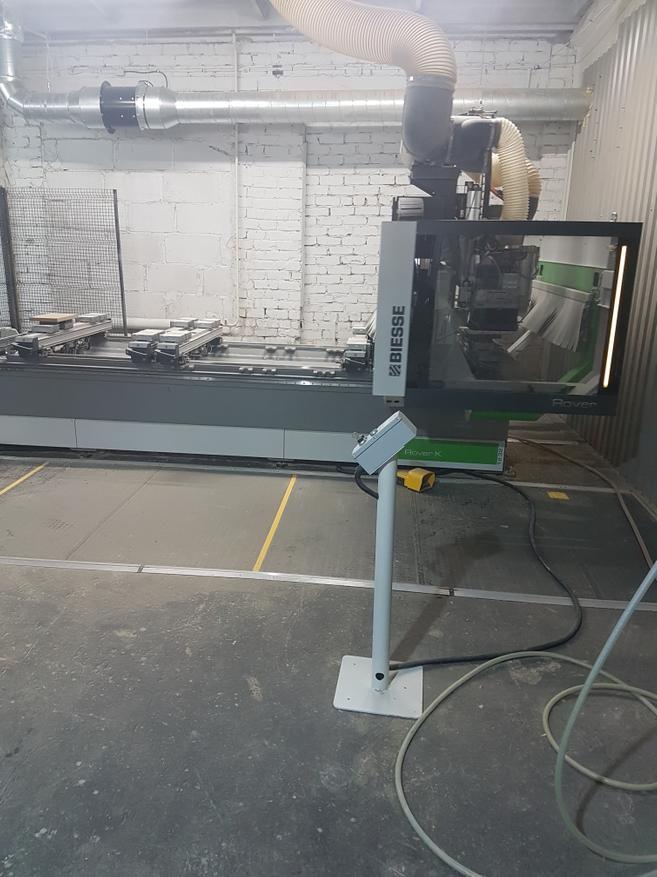
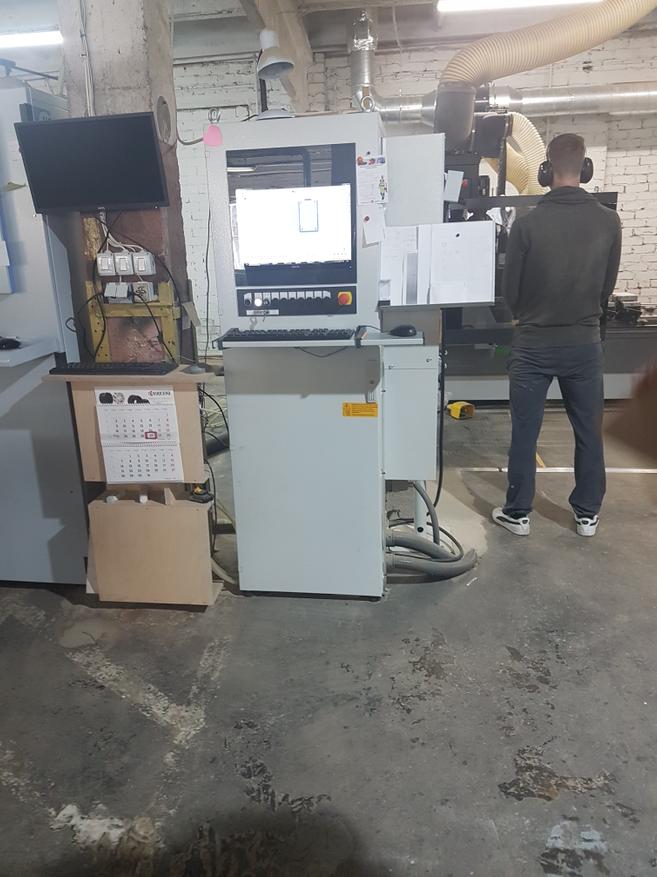
Заготовка превращается в корпус 1
Заготовка превращается в корпус 2
Наиболее эффективно в течение, как минимум, одного дня производить корпуса одной модели. Например, в течение недели делать только корпуса Arslab Classic 3.5 без перенастройки станков с производительностью до 50 корпусов в день. Склейка корпусов производится вручную. На этом этапе производится и приклейка битумного звукопоглотителя в рассчитанных для данной модели местах. Помимо приклеивания, материал крепится степлером.
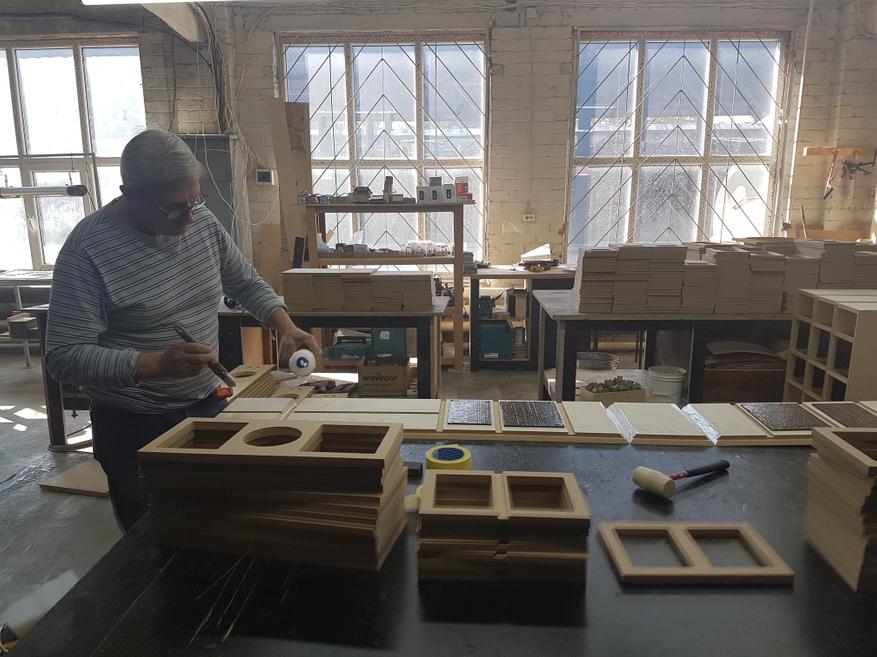
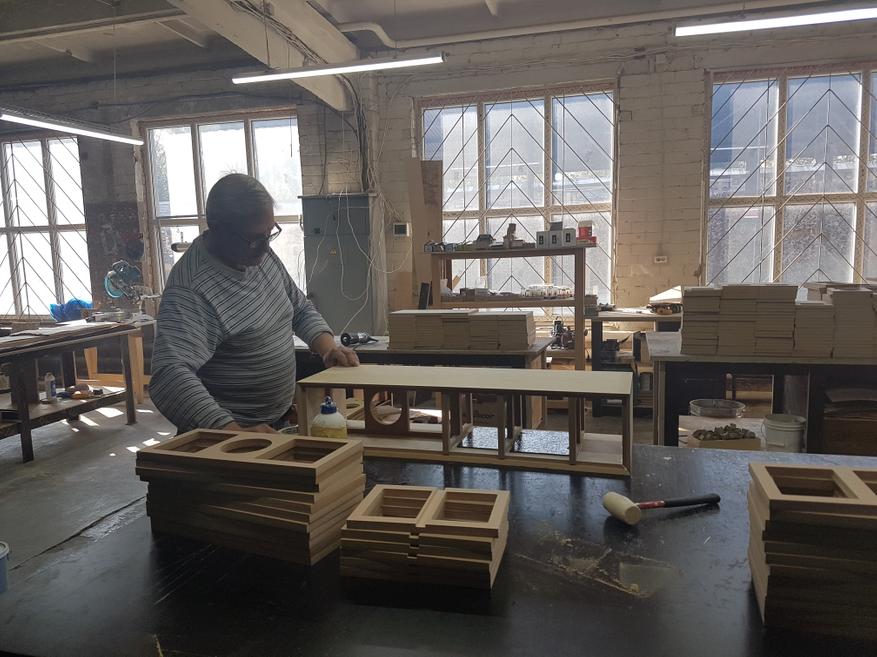
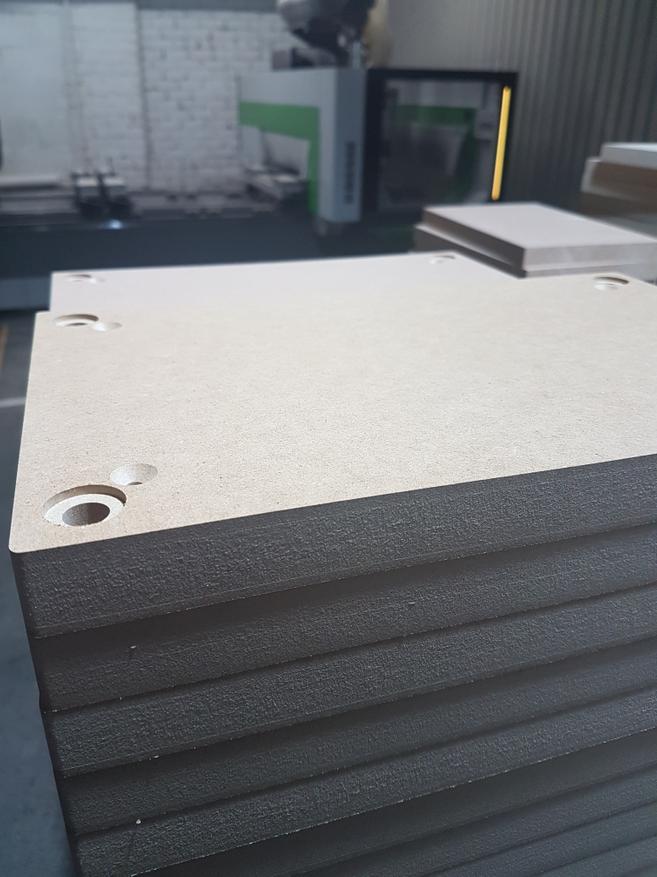
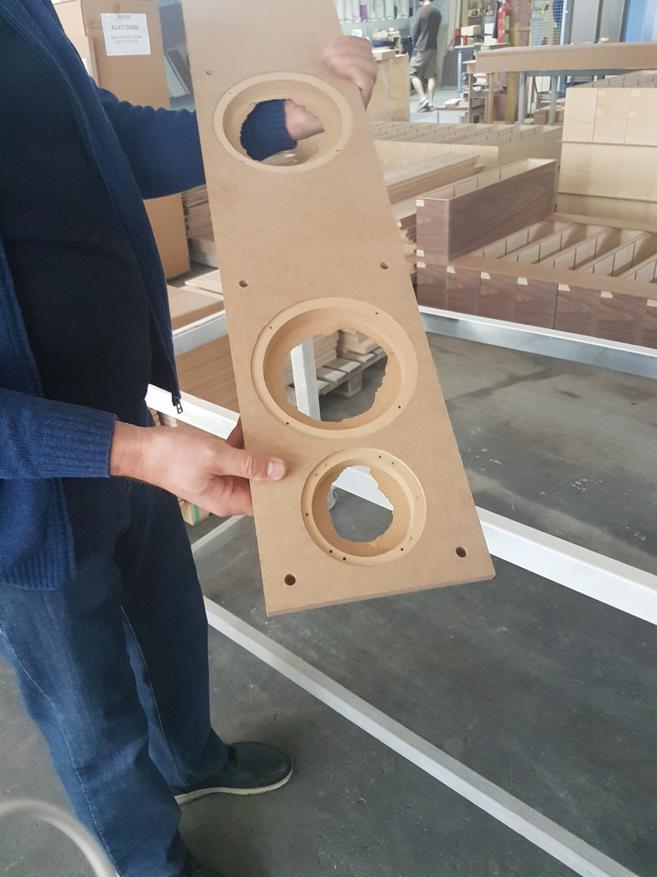
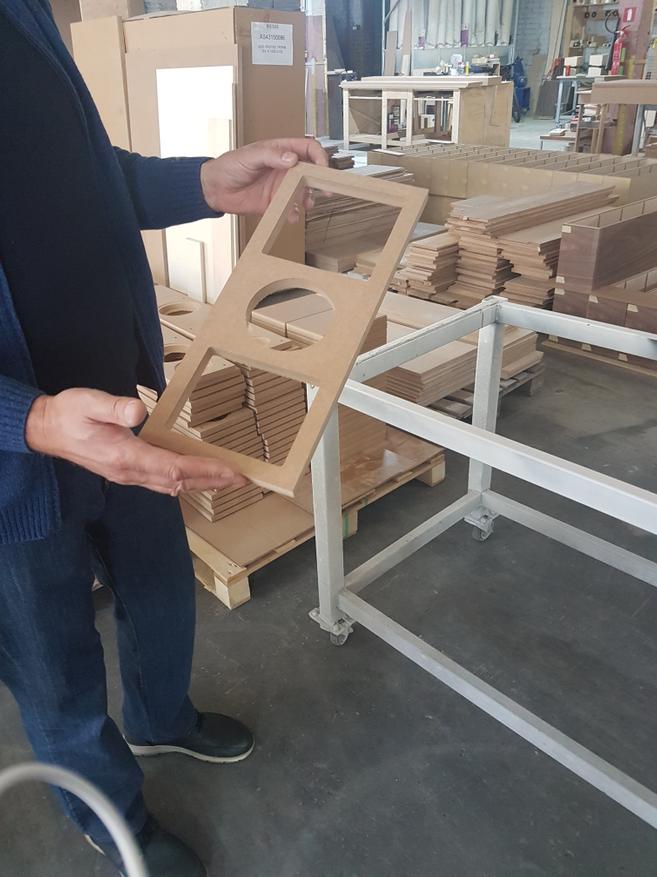
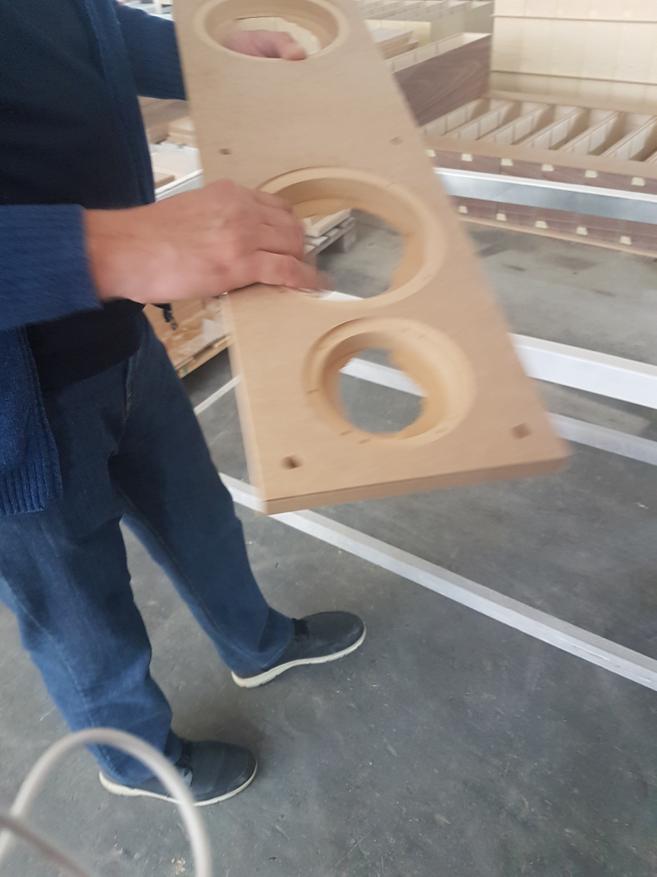
Далее производится грунтовка, шлифовка, окраска в несколько слоёв; в случае отделки натуральным шпоном, также используется дальнейшее нанесение лаков и прозрачных красок. Для каждого вида отделки подобраны соответствующие клеи, лаки и краски.
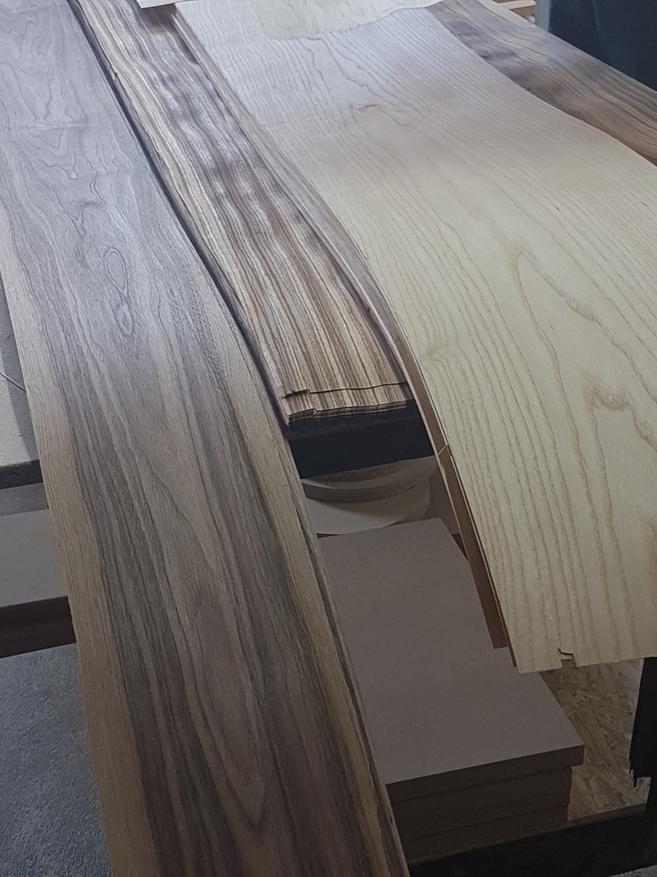
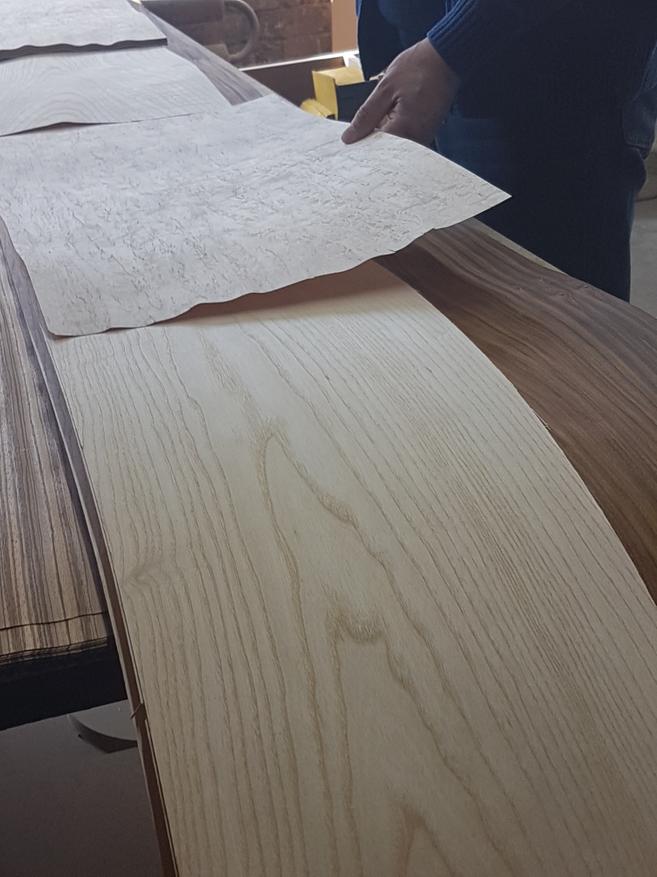
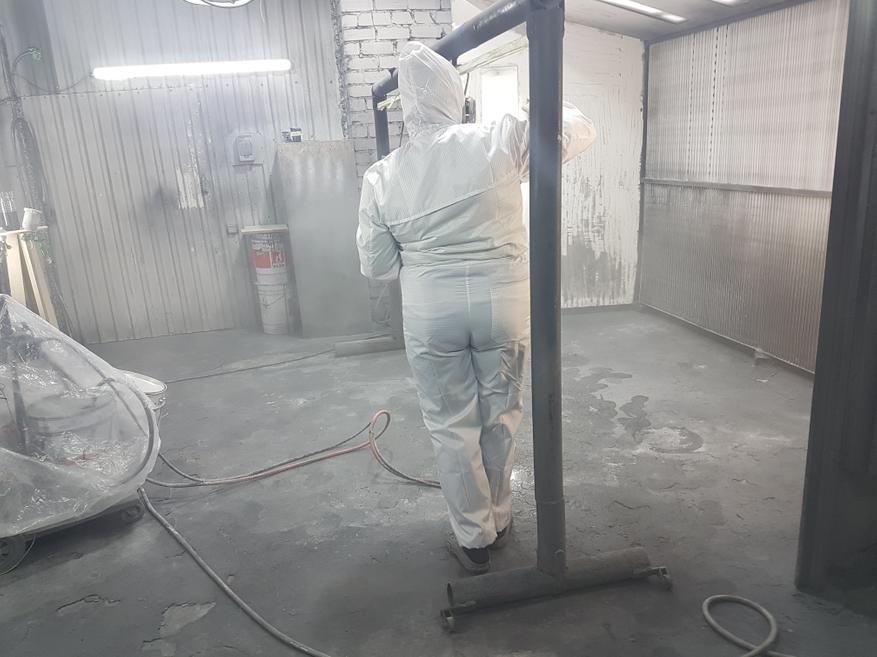
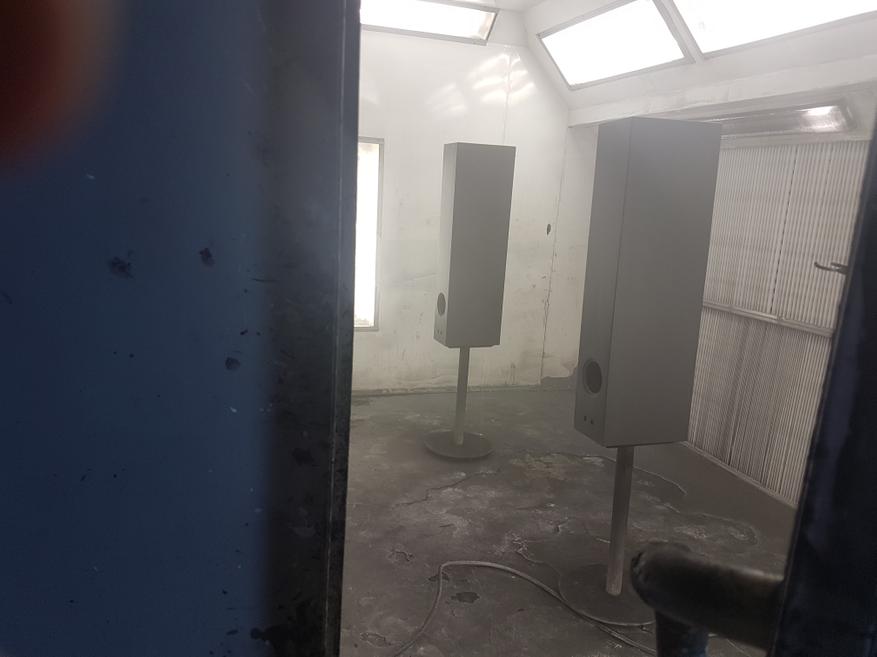
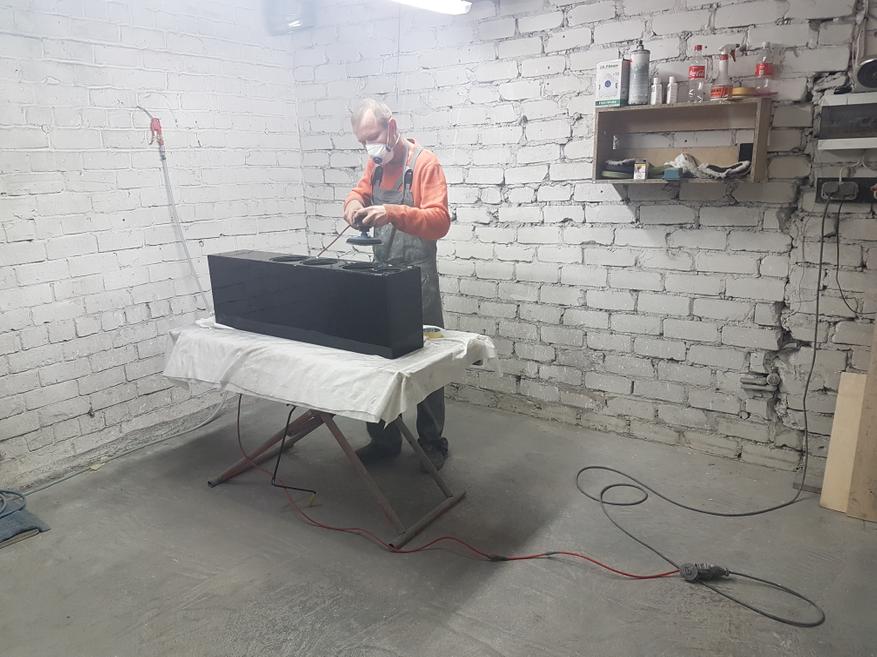
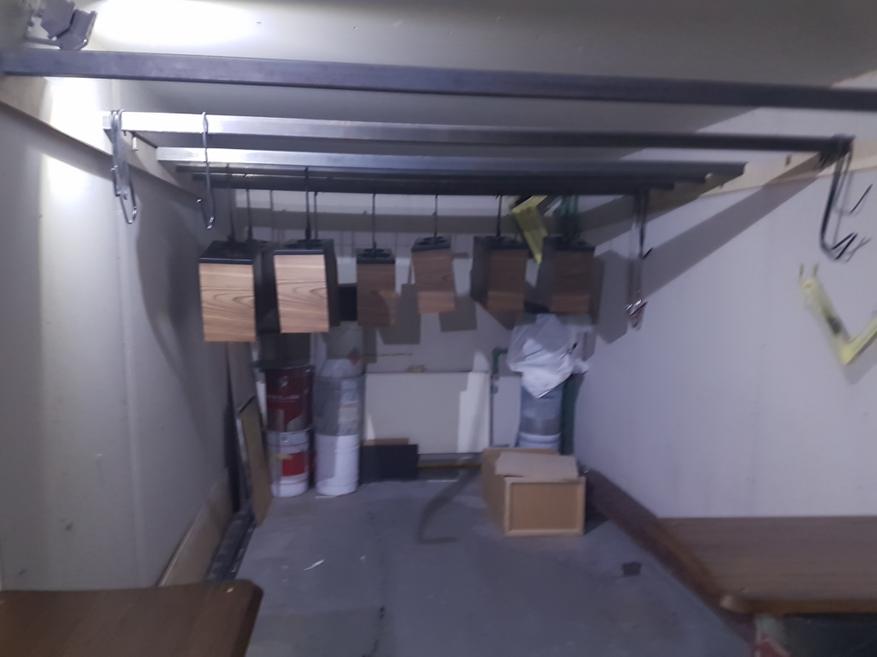
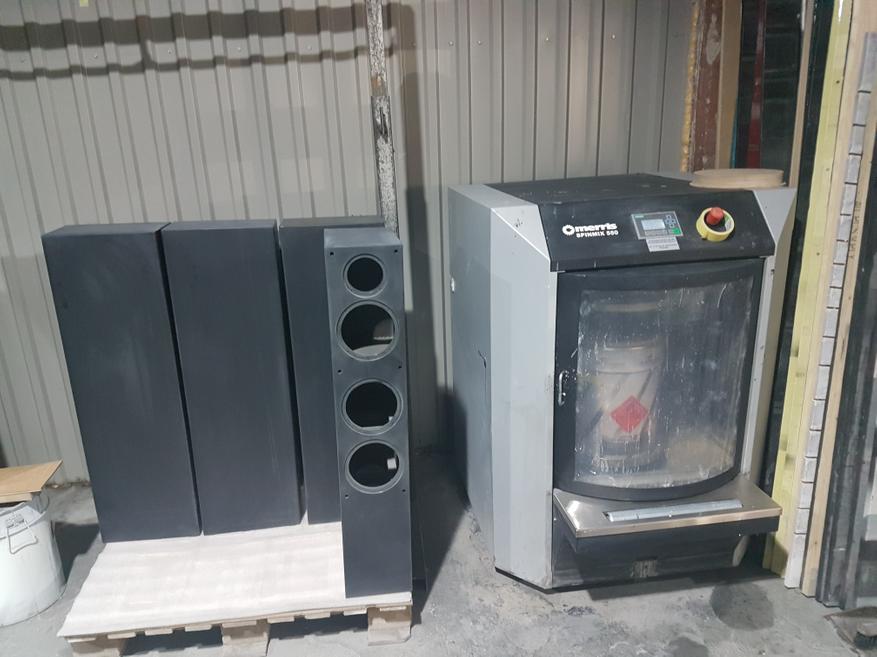
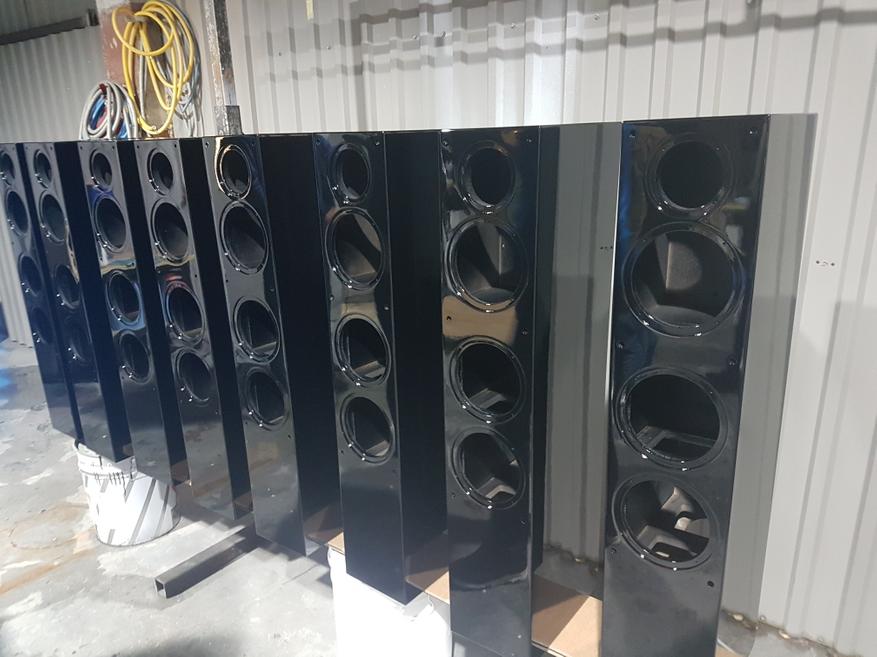
На фото специальная установка для перемешивания краски в 50-килограммовых банках. Это необходимо для достижения стабильности цвета в партии корпусов.
Тонкости процесса, зачем нужно столько слоёв
Используются все возможные пути для получения максимального качества окраски: поддерживается необходимая влажность, вентиляционная система прокачивает огромные объёмы воздуха, используется специальное устройство для снятия пыли и статики с униформы сотрудников, выдерживаются технологические паузы до суток между операциями грунтовки, шлифовки, нанесения слоёв лака или краски; корпуса различных цветов в течение одного дня не красятся. Небольшой процент брака отсеивается контролем качества, корпус полностью перекрашивается. В целом, технология схожа с покраской автомобилей.
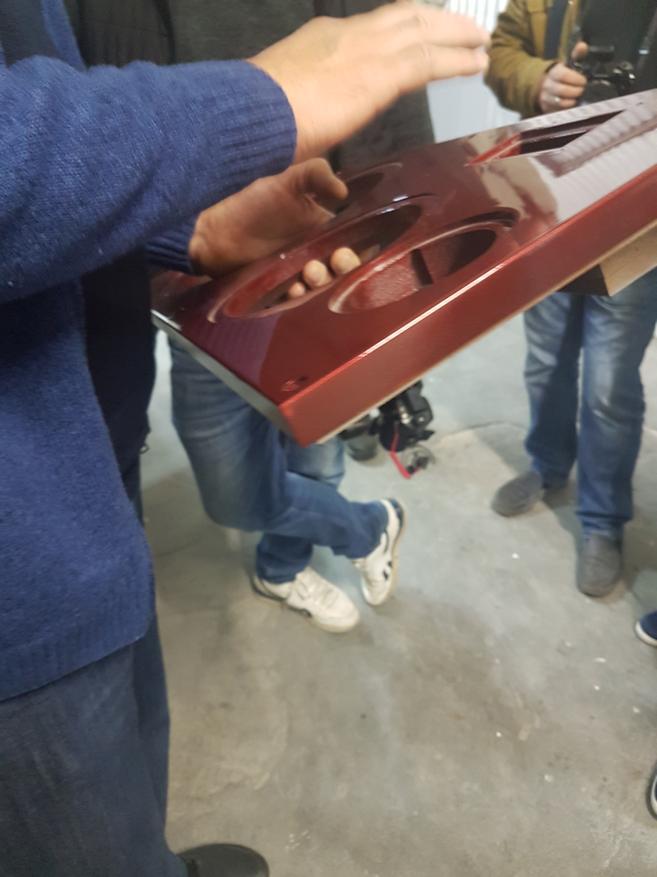
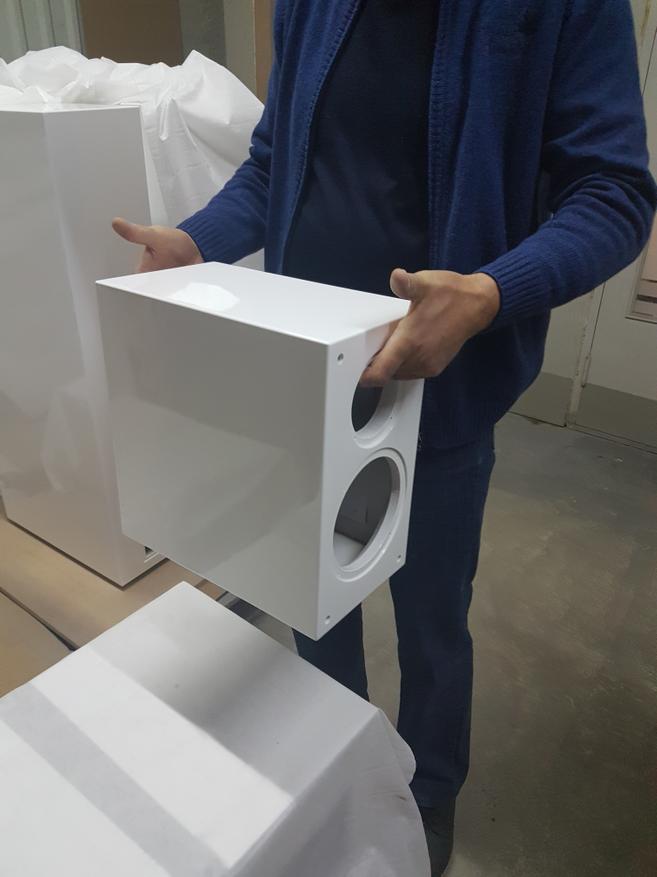
Далее корпуса отправляются на промежуточный склад. Реализован автоматизированный контроль: оператор вводит в планшет приход корпусов, и тут же все данные доступны в московском офисе. Это позволяет планировать и обеспечивать ритмичность поставок и существенно упрощает логистику.
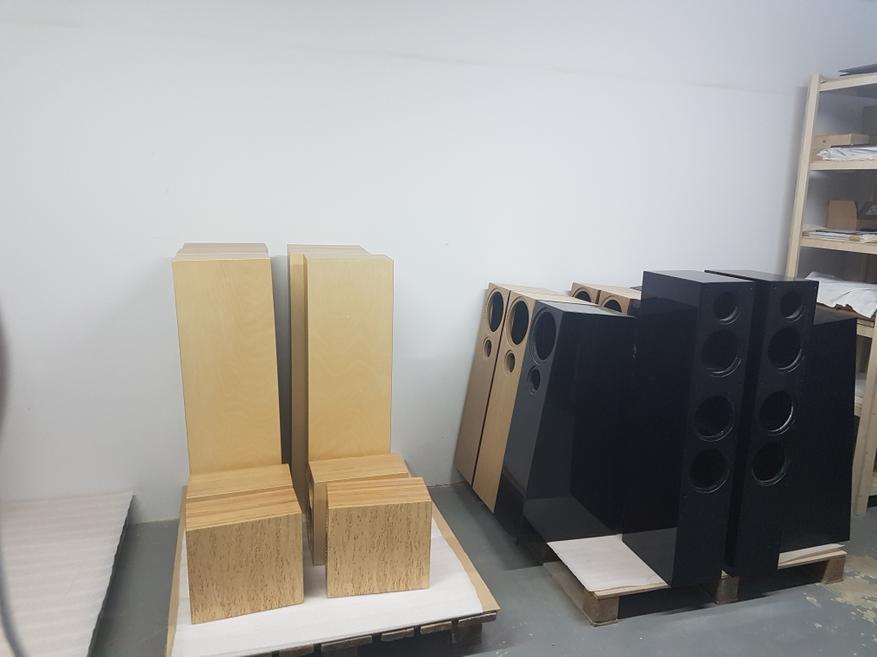
Кроссоверы изготавливаются вручную по технологическим картам конкретной модели. Используются комплектующие Mundorf, Jantzen, Audiocore.
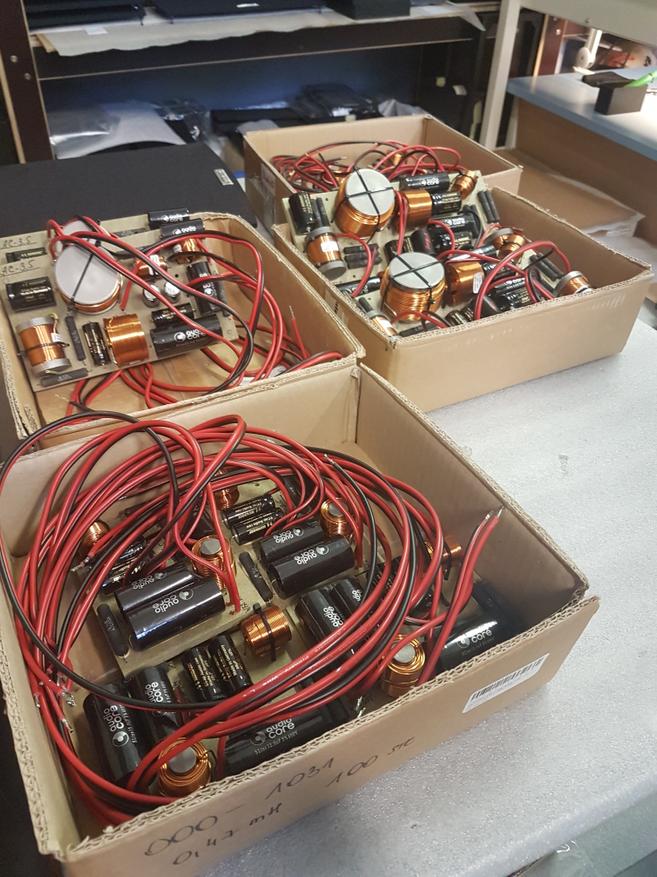
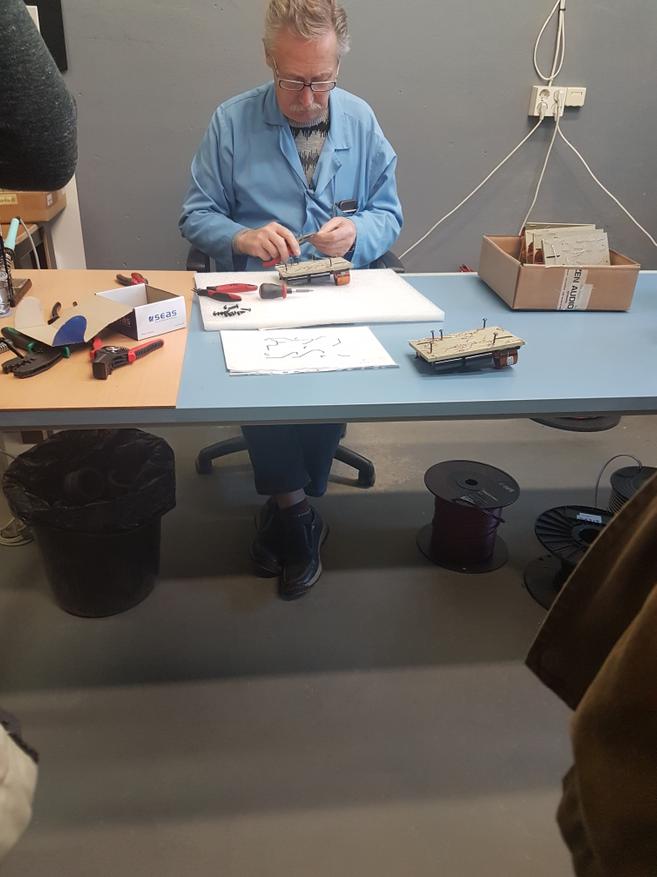
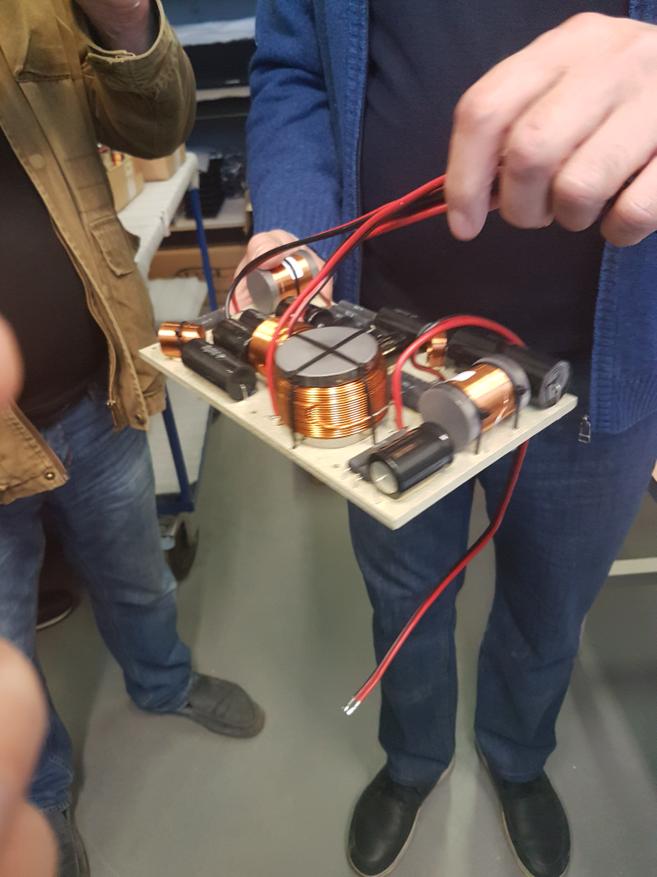
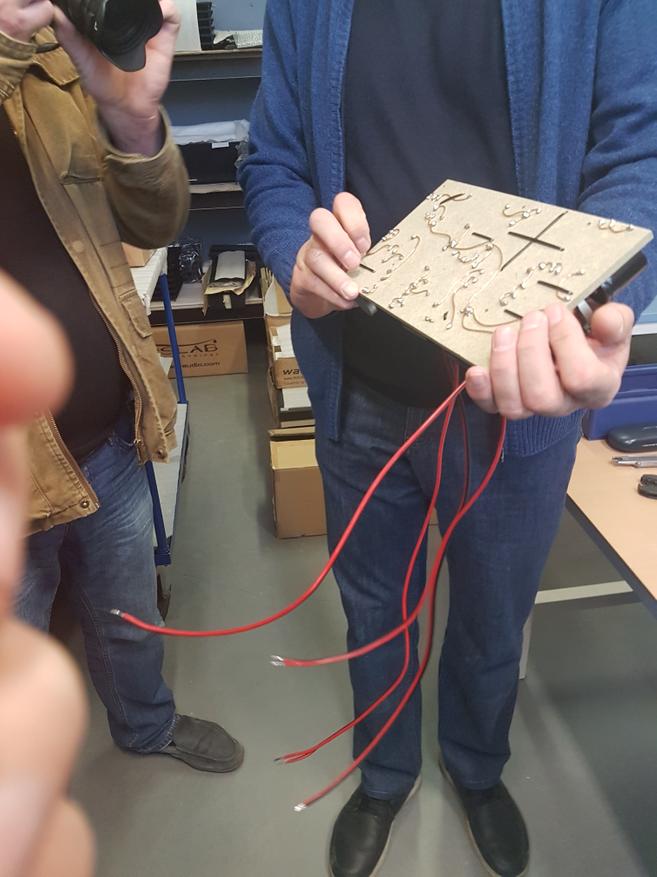
Директор компании «Аудиомания» Артём Фаермарк
демонстрирует набор деталей кроссовера топовой модели акустики
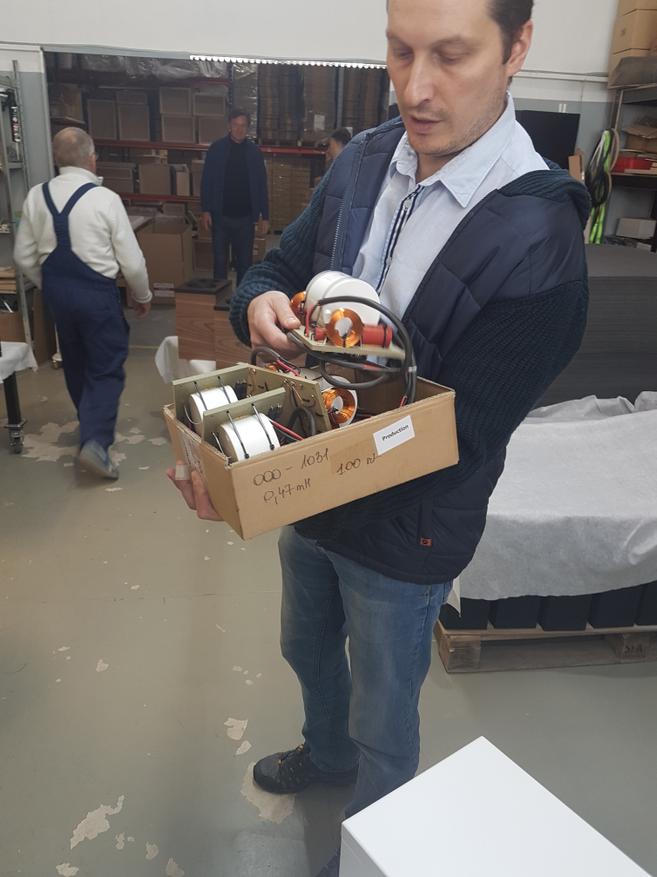
Для внутренней разводки разных моделей акустических систем используют разные акустические провода, в том числе серебряные.
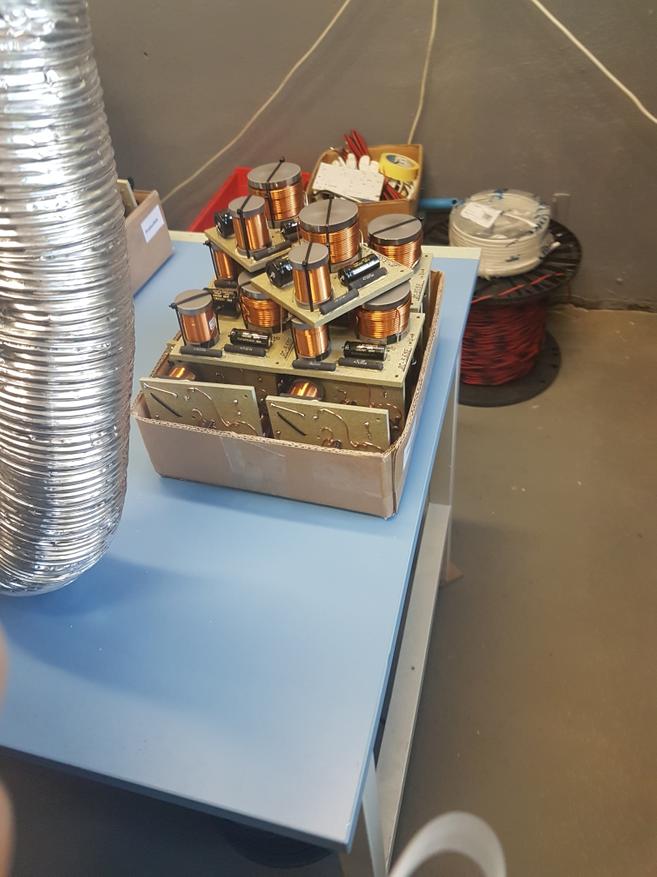
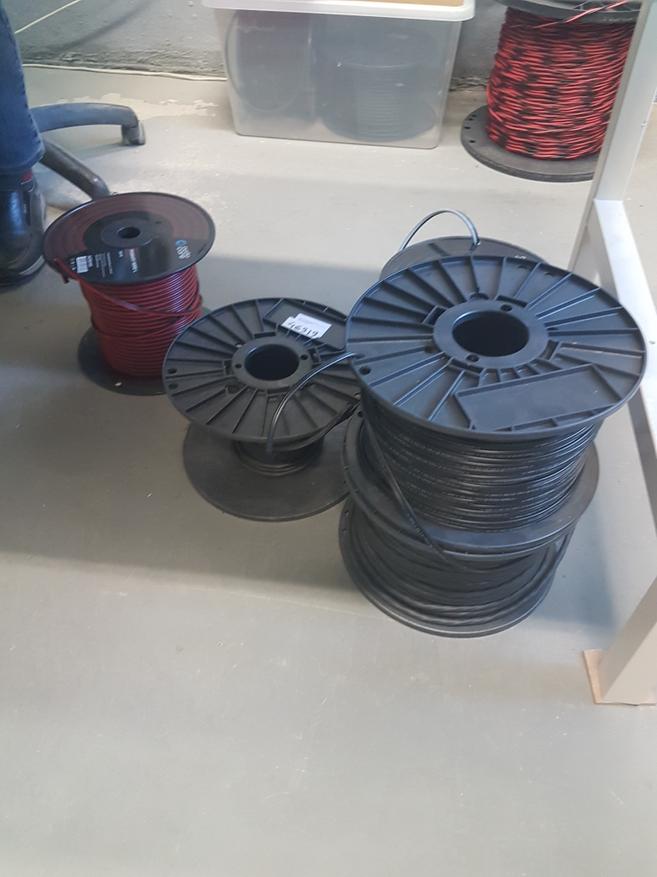
Следующий этап — ручная установка всех комплектующих в корпус. Динамики закупаются у пяти проверенных поставщиков: Seas, Wavecor, Sica, Morel, Beyma. Есть договоренности с некоторыми из них о заказе партий динамиков под нужные спецификации и даже единичных экземпляров для экспериментов. На этом этапе в корпус укладывается и прикрепляется звукопоглотитель одного из четырёх видов.
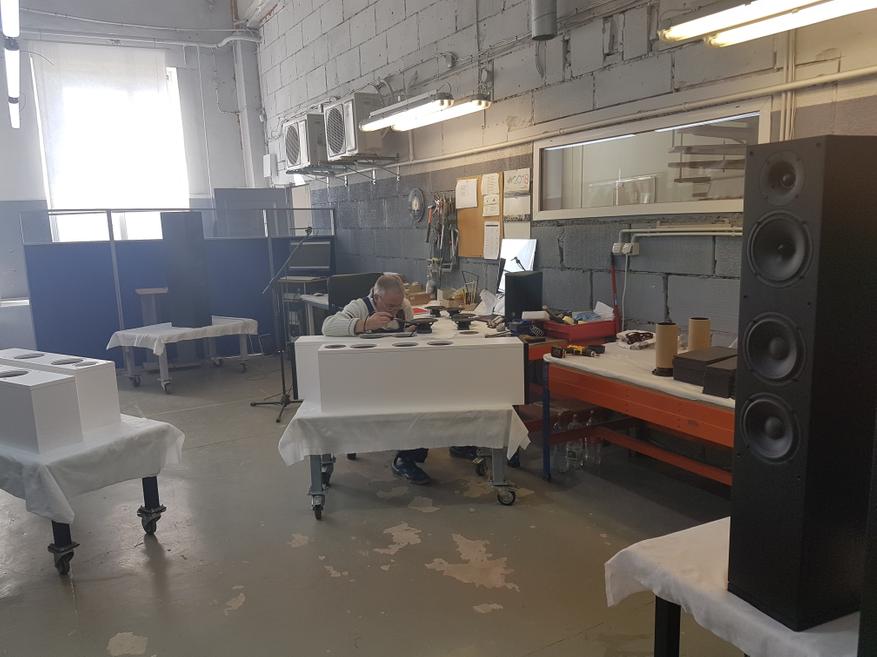
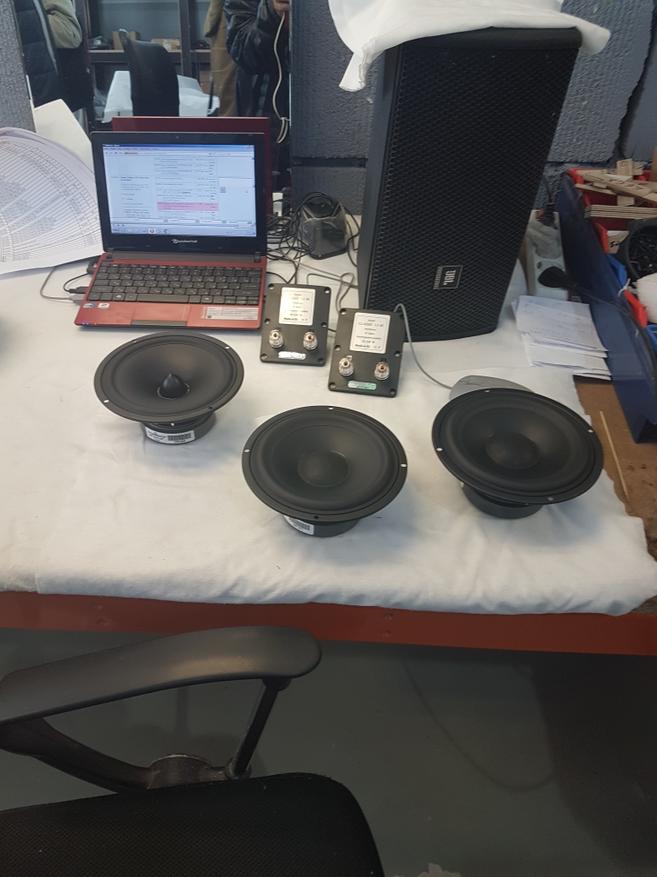
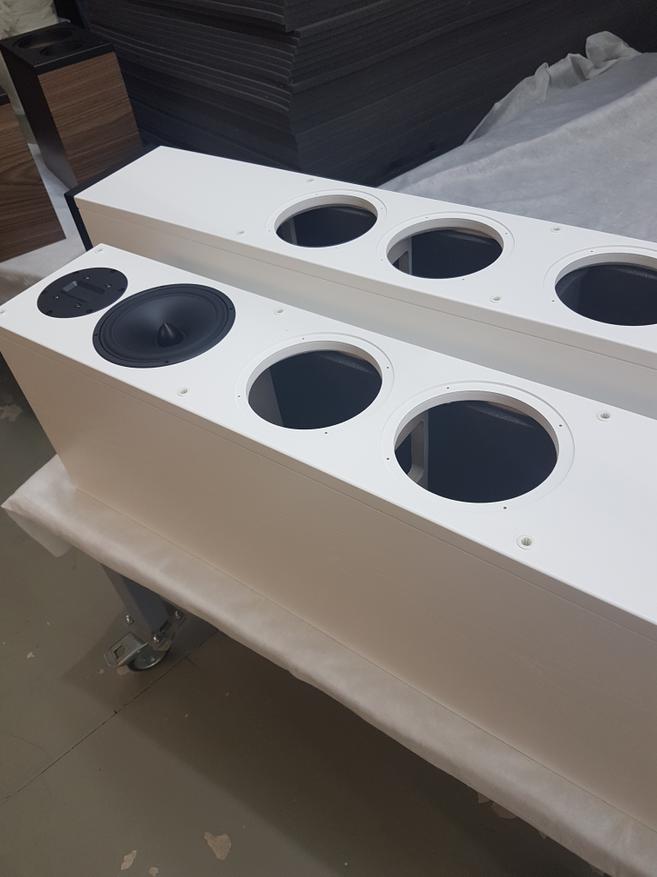
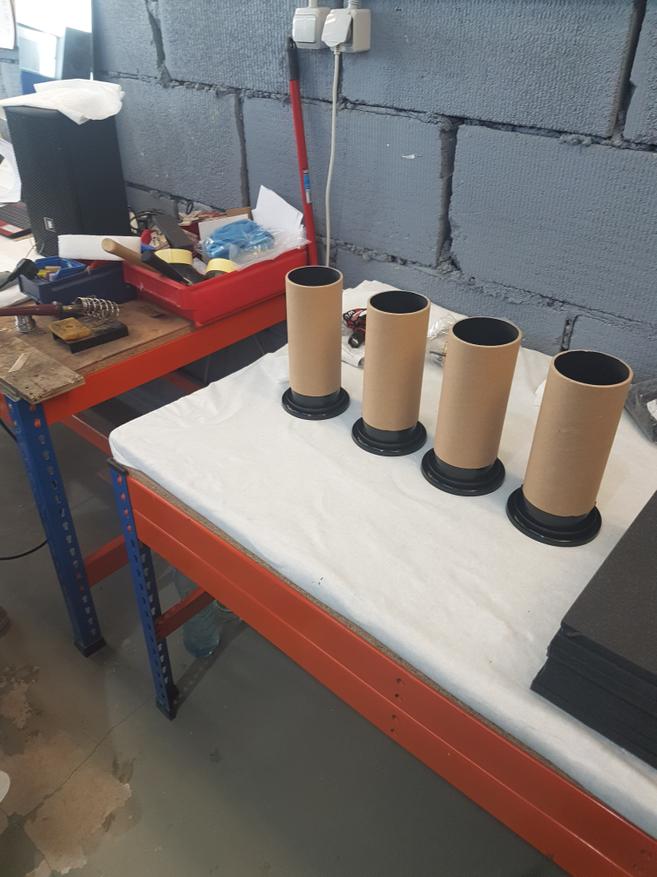
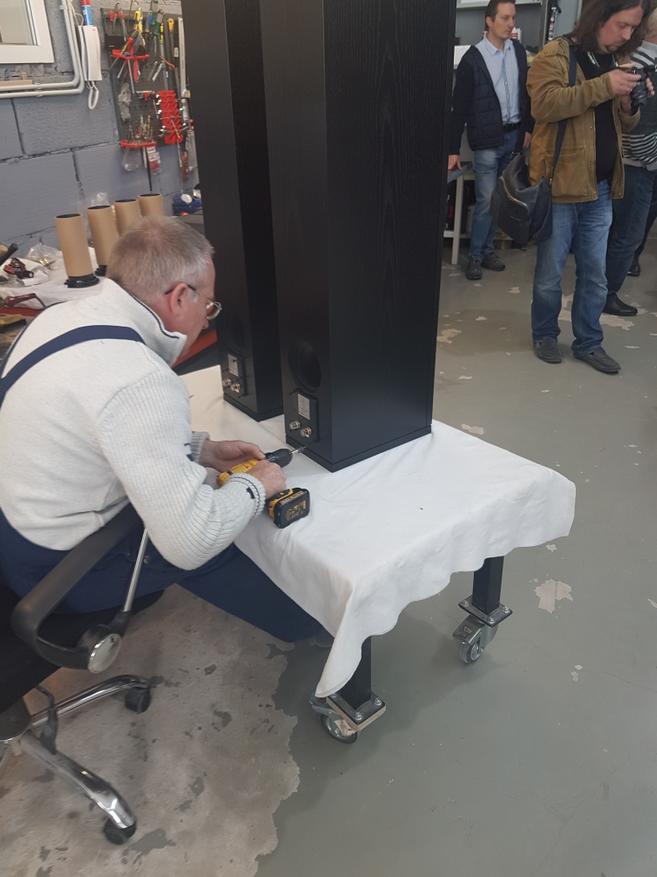
Перед упаковкой АЧХ каждого изготовленного экземпляра сравнивается с эталонным графиком характеристики для данной модели.
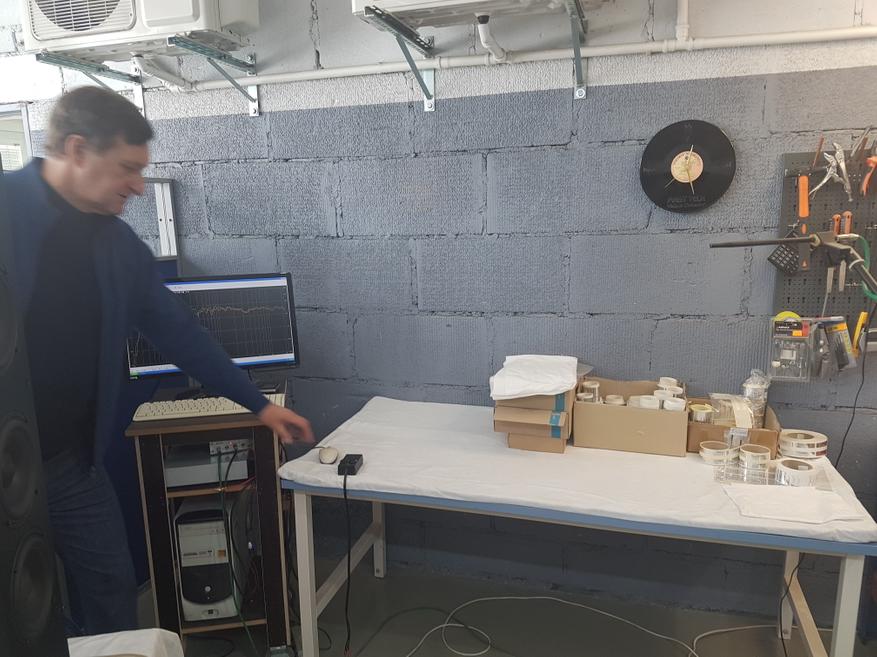
На каждую колонку из пары наклеиваются защищенные голографические, саморазрушающиеся при снятии наклейки с номерами, и номера в паре следуют подряд.
Упаковка продукции, производимой Аудиоманией, мне всегда нравилась. Как визуально (картонные ящики на прочном каркасе, собранные на саморезах, и другие признаки милитари-стилистики), так и с точки зрения практичности и сохранности продукции.
Мне удалось запечатлеть процесс создания внутренней упаковки акустики:
Склад готовой продукции
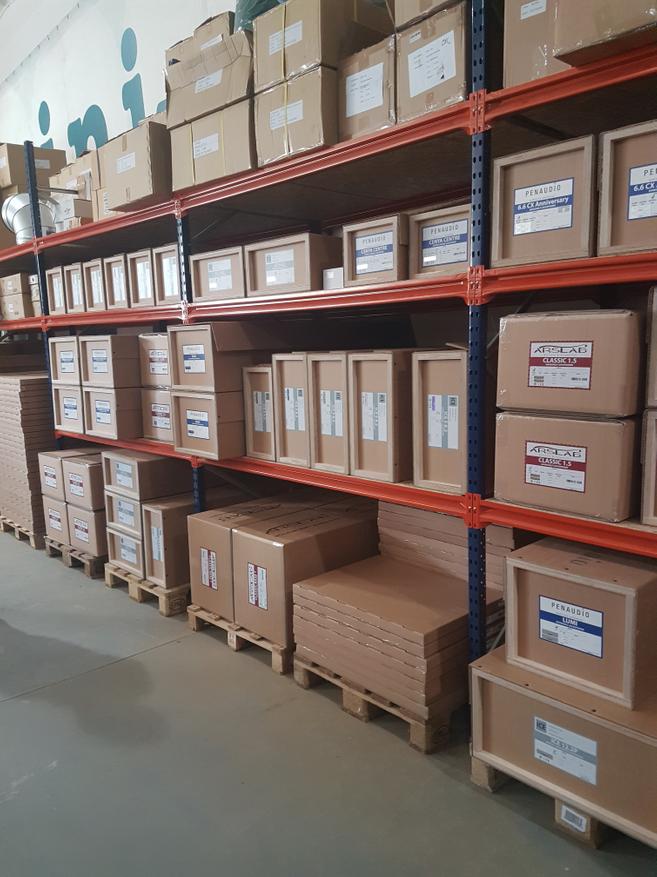
Четыре часа экскурсии по фабрике пролетели незаметно. За кадром остались некоторые ноу-хау фирмы, а некоторые тонкости изготовления, например, различные варианты перекрещивания слоёв древесины и варианты демпфирования корпусов являются слишком узкоспециализированной информацией. В целом, на фабрике меня поразило общее качество организации процесса производства, оптимальный темп работы и ритмичность. При этом имеется возможность быстрой переналадки процесса и запуска другой модели в том же повторяемом качестве. Владелец фабрики Артём Фаермарк, технический директор Виктор Лагарпов, а также конструктор Юрий Фомин дали исчерпывающие ответы на все вопросы. Меня порадовала культура и организация производства, а также общая атмосфера на фабрике, чувствуется что каждый из сотрудников стремится к наилучшему результату работы.
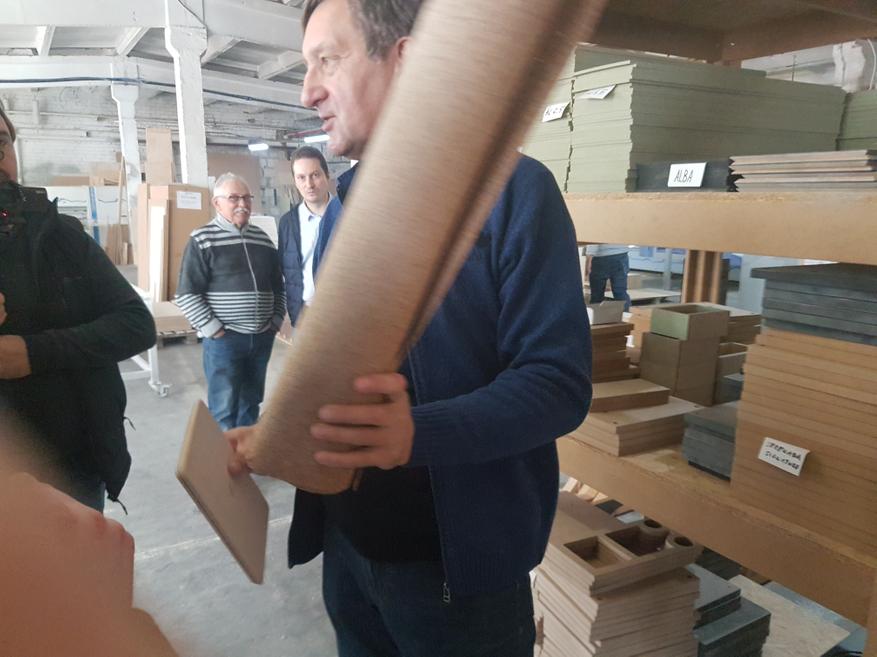
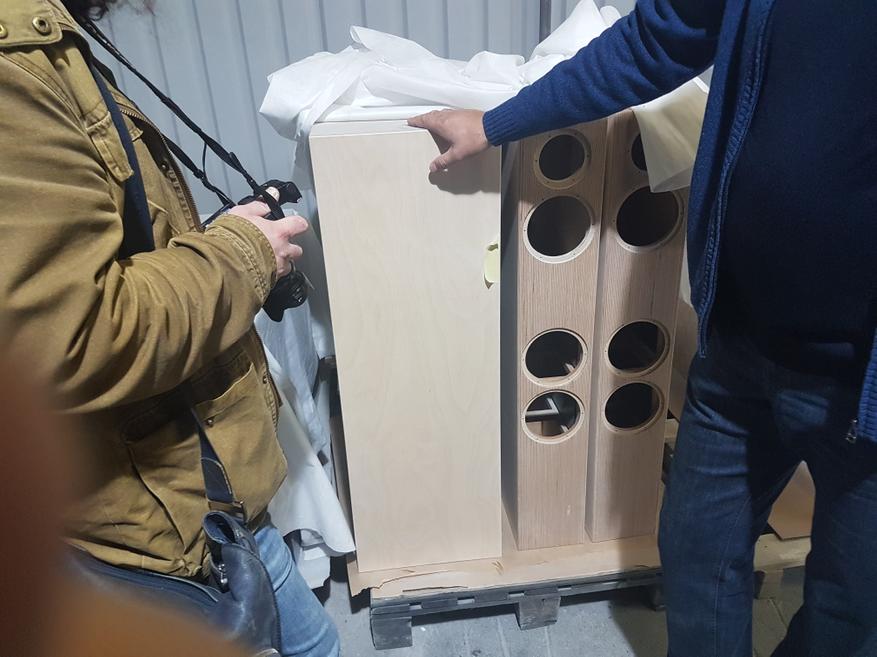
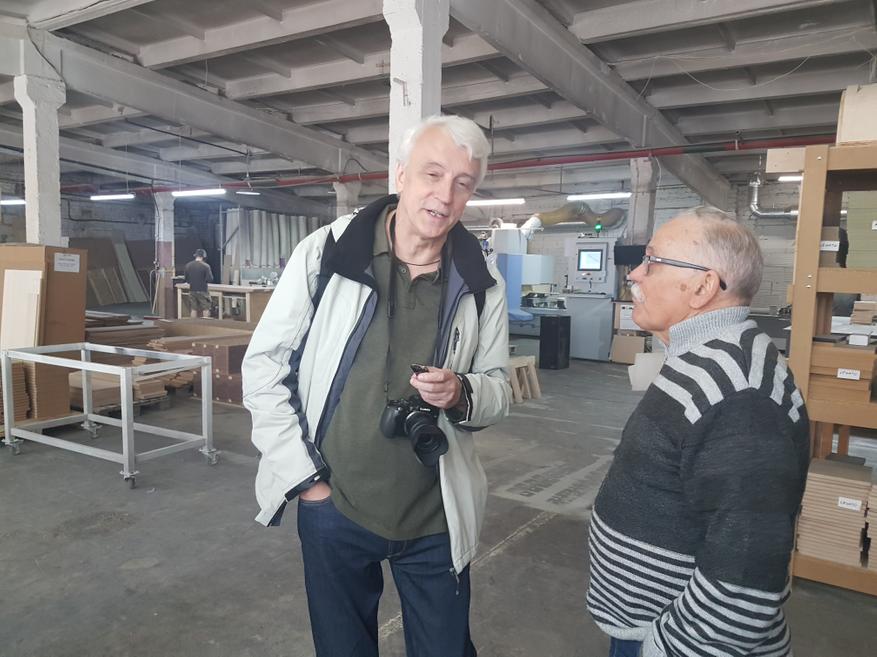
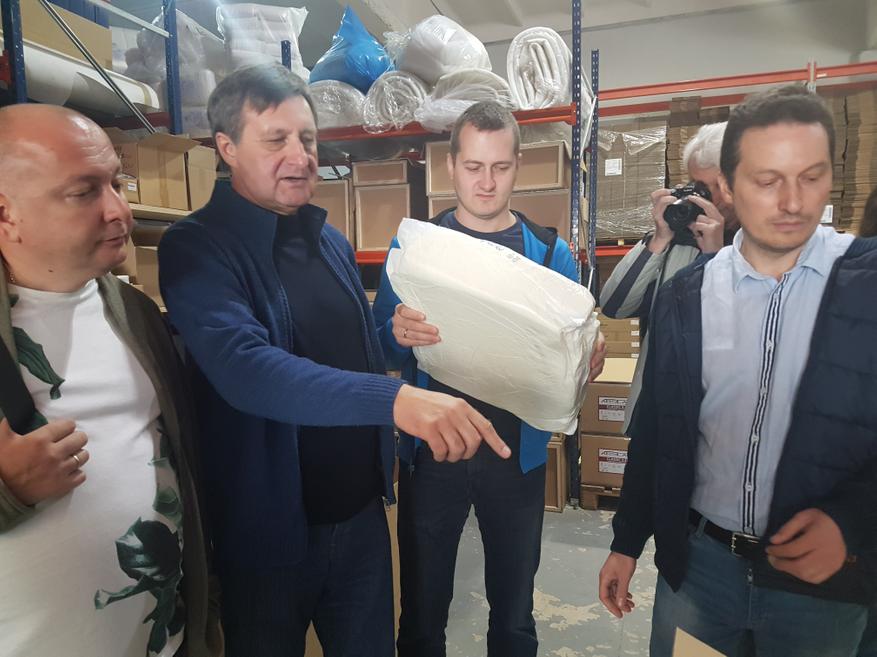
Выражаю благодарность компании «Аудиомания» за приглашение и надеюсь, что мой краткий репортаж был интересен меломанам и аудиофилам.
74 комментария
Добавить комментарий
У серебра как бы самая лучшая электропроводность из металлов…
Про разработку… так это ж фабрика по производству, а не R&D департамент.
Завтра или послезавтра их обзор выйдет.
https://www.youtube.com/watch?v=KbW7pjwRc-w
Добавить комментарий